Infuser PRG®
Fully Automatic Injection System
Ultimate RTM Injection System.
The Infuser PRG® is a fully automated RTM injection system providing state-of-the-art features and innovation to exceed your daily production demands. JHM Technologies' Infusatrol injection software removes operator error and increases product repeatability by placing, the process control within secured pre-configurable "recipes". Never before has an injection system proactively monitored the flow rate, injection pressure, resin temperature, catalyst ratio, and elapsed injection time in order to ensure a production quality finish from the mold.
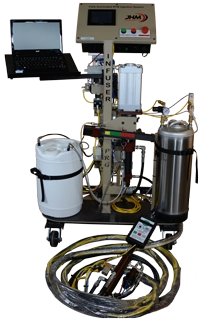
Pull Parts up-to 60% Faster
Infuser PRG is equipped with the revolutionary Automatic Catalyst Ratio (ACR) control, reducing part curing times by up to 60%! This industry-changing feature provides precise—free from operator error—programmable control over the catalyst levels throughout the injection period.
Eliminate Voids & Post Mold Rework
With the latest version of JHM Technologies Infusatrol software, the Infuser PRG® proactively monitors the flow rate, injection pressure, resin temperature, catalyst ratio, and elapsed injection time to ensure the injection is inline with the preconfigured specification. Precise control throughout the entire injection process leading to void elimination and post mold re-work.
Reduce Resin Usage
No more wasted resin! Infusatrol's Flow Control provides precise control over the amount of resin used when filling the mold. Proven using documented industry averages to reduce resin usage up-to 20%! Monitoring the pressure alone can not match the performance of Infusatrol's Flow Control.
Companies Rely on the Infuser PRG® to Succeed
Thomas Goodrich
RTM/Nema Molding Dept. Supervisor
From monitoring the cavity vacuum to variable catalyst ratio the control built into the Infuser PRG® is unbelievable!
And to talk about the repeatability!!!
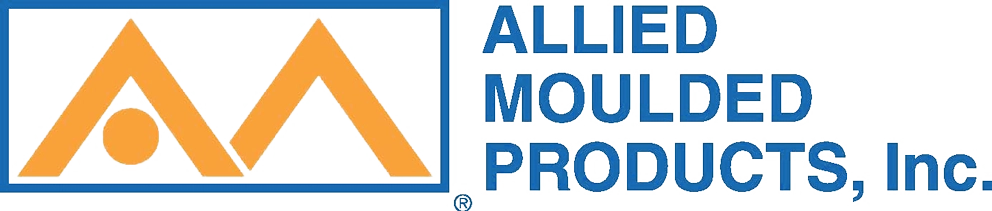
Thomas Goodrich
RTM/Nema Molding Dept. Supervisor
I've been using the Infuser PRG® for over 7 years and I can't speak highly enough on how much value this machine has added to our product! Allied Moulded Products Inc. has been in business for over 55 years and I believe that would not have been possible without paying attention to details. Allied had farmed out LRTM work for our larger electrical enclosures that we had made for several years moving from one vendor to the next. Most all of the venders we used claimed that they were unable to turn a profit. After viewing first hand some of the crude processes our vendors used to manufacture our enclosures it was clear to me that that they had no process control. Allied decided to take matters into their own hands and start it’s very own LRTM process bringing all our molds in house.
My first order of business was to figure out a way to gain process control in a process that is somewhat imprecise. We found JHM Technologies and discovered that John Moore and his team were very detailed oriented especially in the design of the Infuser PRG® injection system. Coming from a compression and Injection molding background I knew the repeatability is key to any molding operation. Because LRTM is such a manual process I knew that gaining as much process control as possible was the only way to make a profit. In this day and age of “smart” technology I would have to say John and his team were way ahead of the trend. From monitoring the cavity vacuum to variable catalyst ratio the control build into the Infuser PRG® is unbelievable! And to talk about repeatability!!! My goodness the idea of mold tags for all my molds which keeps my shots the same day in and day out no matter who is pushing the buttons is unreal!
I know the argument is "with more bells and whistles comes more problems" which might be true, but I think anyone would agree that with a good preventative maintenance program (which the JHM Technologies machine tracks) planned or unplanned maintenance is a lot easier to control cost over unexplainable scrap or post part repair. Which leads me right into JHM Technologies customer support; John and his team understand the pressures of being a manufacturer and are always willing to go the extra mile to help you solve a problem be it maintenance of the machine to process related issues. I remember being at our sister company in India... yes India where we are also using a Infuser Series injection system. There was a particular problem that I was helping my Indian co-workers trouble shoot and I was a bit stumped. John was just a call away from getting them up and running again, that's what I call knowing your equipment!
5 of 5 Resin transfer molding injection system!
Mithum Mandal
Certified Composites Technician
We never imagined an injection system—like the Infuser PRG®—being this simple to use! We will be purchasing another Infuser Series machine in the future.
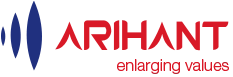
Mithum Mandal
Certified Composites Technician
It's amazing to have your Infuser PRG® injection system in our facility. The Infuser PRG® is perfectly made to suit a production environment that requires security and restrictions on changing parameters.
The features are amazing; allowing us to infuse parts in less time and monitoring different parameters like flow rate, injection temperature, injection pressure. The parts coming from the Infuser PRG® are much higher quality than previous parts we were infusing with a different injection system.
We were right in purchasing an Infuser Series injection system! The online training provided by JHM Technologies showed us just how easy these injection systems are to use. We never imagined an injection system—like the Infuser PRG®‐being this simple to use.
We are now ready for production and will purchase another Infuser Series machine in the future!
The politeness & co-operation from the JHM Technologies team is really appreciated. Our team and managements thanks you for your co-operation and valuable suggestions you have given us online, which has helped us a lot. We again thanks you!
5 of 5 Closed molding injection system!
Justin Achard
Composite Tooling Engineer
Infuser PRG® has enabled us to produce quality parts while providing us with traceability through the data collection system!

Justin Achard
Composite Tooling Engineer
Technical knowledge and co-operation has been vital to the successful relationship that exists between JHM Technologies and McGard / L.D. McCauley. The Infuser PRG® injection system designed and built by JHM Technologies enabled us to quickly produce quality parts while providing us with traceability through the data collection program provided. We were able to use this system to take our product from research and development to full production very quickly.
We are extremely pleased with the reliability of the injection equipment. Your expertise has helped us tremendously.
I would highly recommend JHM Technologies, over its competitors, to anyone in the composites industry.
5 of 5 Injection system!
Features
Infuser PRG® Features
- Proactive Injection Monitoring
- Infusatrol®'s recipes provide the Infuser PRG® with complete automation of the injection process. Using pre-configured mold recipes the Infuser PRG® will proactively monitor the flow rate, injection pressure, resin temperature, catalyst ratio, and elapsed injection time in order to assure a precise and repeatable injection. This level of proactive control allows the Infuser PRG to not only monitor but also correct the injection process.
- Progressive Catalyst Ratio (PCR)
- PCR drastically improves demolding time by providing linear control over the catalyst to resin ratio—from 0.5% to 3%—through the injection process. PCR configures the catalyst ratio to increase during the injection process resulting in an even cure across the mold.
- Catalyst Monitoring
- To eliminate the chance of a catalyst-free part, the Infuser PRG® monitors the catalyst for proper flow and ratio throughout the injection process. Upon an issue arising the Infuser PRG® will halt the injection and notify the operator of the catalyst issue.
- Automatic Flush
- The Infuser PRG®'s automatic flush is designed to eliminate the chances of "gumming up" the injection system, by detecting when a flush is required. Using its air-solvent purge system the Infuser PRG® will detect, alert, and even automatically flush—when configured to.
- Cavity Vacuum Monitoring
- Remove post work due to air bubbles from you injection process! Infuser PRG®'s cavity vacuum monitoring senses the vacuum level within the mold cavity and provides real time feedback. Using Infuseatrol's recipes the Infuser PRG is able to delay the injection due to low vacuum levels and alert the operator during injection.
- Fully Upgradeable
- The modular design of the Infuser PRG® allows for easy integration with future innovations within the Infuser Series. Upgrade your injection system without having to purchase a completely new one!
Models
Infuser PRG® Models
Infuser PRG®
Standard two component fully-automatic RTM injection system, designed for polyester and vinylester resins. Equipped with a 100cc resin pump and infinitely adjustable 4.5cc stainless steel catalyst pump.
- 100cc Hardened resin pump
- 4.5cc Stainless steel catalyst pump
- 25 ft. Industrial grade hose set
- 5 gal. Stainless steel solvent tank
- Stainless steel braided catalyst lines
- Visual catalyst level warnings
- Programmatically adjustable—prior to and during injections—catalyst ratio
- Automatic injection head with significantly reduced mix waste
- Automatic resin recirculation
- Removable NRV valve for ratio checking
- Absolute electronic MPG injection pressure sensor
- Electronic pump speed regulator
- Electronic resin pressure regulator
- 6 in. Backlit mono-color touch screen display
- Industrial grade alarm system to notify operators of alerts, conditions, and more.
- Multilevel user interface with password protection
- Configurable automatic injection and flush cycles
- Configurable inputs for actual injection pressure and volume
- Cavity vacuum monitoring—with confirmation prior to injection
- Closed loop PID control of injection flow rate
- Injection pressure limit governor
- Injection recipes (99 recipes, extensible to unlimited with data collection system)
- Machine usage logs for preventative maintenance
- Mounted on floor stand with industry grade swivel wheels for easy movement
- 110V 3AMP control unit
- 220V 11AMP heater unit
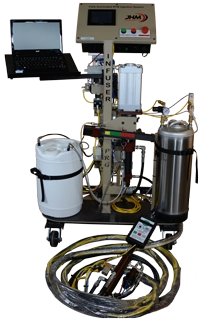
Infuser PRG® EPX
Two component full-automatic RTM injection system design for epoxy and urethane resins. Equipped with a 100cc resin pump and a 50cc hardener. Along with moisture locking hoses as standard—preventing reaction with environmental sensitive hardeners.
- 100cc Resin pump
- 50cc Hardener pump with adjustable ratio
- 25 ft. Industrial grade hose set
- 5 gal. Stainless steel solvent tank
- Stainless steel braided catalyst lines
- Visual catalyst level warnings
- Automatic injection head with significantly reduced mix waste
- Automatic resin recirculation
- Removable NRV valve for ratio checking
- Absolute electronic MPG injection pressure sensor
- Electronic pump speed regulator
- Electronic resin pressure regulator
- 6 in. Backlit mono-color touch screen display
- Industrial grade alarm system to notify operators of alerts, conditions, and more.
- Multilevel user interface with password protection
- Configurable automatic injection and flush cycles
- Configurable inputs for actual injection pressure and volume
- Cavity vacuum monitoring—with confirmation prior to injection
- Closed loop PID control of injection flow rate
- Injection pressure limit governor
- Injection recipes (99 recipes, extensible to unlimited with data collection system)
- Machine usage logs for preventative maintenance
- Mounted on floor stand with industry grade swivel wheels for easy movement
- 110V 3AMP control unit
- 220V 22AMP heater units
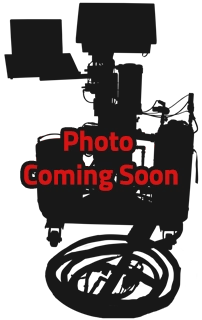
Infuser PRG® 3C
Three component fully-automatic RTM injection system featuring a 100cc resin, 50cc hardener, and 4.5cc peroxide catalyst pump. The Infuser PRG 3C is specifically designed to handle hybrid urethane/vinylester materials. Comes standard with moisture locking hoses—preventing reaction with environmental sensitive hardeners.
- 100cc Resin pump
- 50cc Hardener pump with adjustable ratio
- 4.5cc Stainless steel catalyst pump with adjustable ratio
- 25 ft. Industrial grade hose set
- 5 gal. Stainless steel solvent tank
- Stainless steel braided catalyst lines
- Visual catalyst level warnings
- Automatic injection head with significantly reduced mix waste
- Automatic resin recirculation
- Removable NRV valve for ratio checking
- Absolute electronic MPG injection pressure sensor
- Electronic pump speed regulator
- Electronic resin pressure regulator
- 6 in. Backlit mono-color touch screen display
- Industrial grade alarm system to notify operators of alerts, conditions, and more.
- Multilevel user interface with password protection
- Configurable automatic injection and flush cycles
- Configurable inputs for actual injection pressure and volume
- Cavity vacuum monitoring—with confirmation prior to injection
- Closed loop PID control of injection flow rate
- Injection pressure limit governor
- Injection recipes (99 recipes, extensible to unlimited with data collection system)
- Machine usage logs for preventative maintenance
- Mounted on floor stand with industry grade swivel wheels for easy movement
- 110V 3AMP control unit
- 220V 22AMP heater units
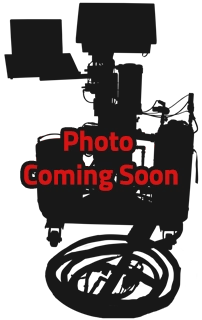
Pricing & Leasing
Infuser PRG® Pricing and Leasing Details
- Buy Direct
-
The Infuser PRG® is available directly from JHM Technologies, Inc. Configured to your exact needs and built in Fenton, MI, USA.
Contact us today for your FREE quote on an Infuser PRG®. - Lease
- Contact us today for details on how you can lease the Infuser PRG®.