VARTM Process Questions Answered
- What is Vacuum Assisted RTM?
- How does the VARTM process work?
- What are the main advantages of VARTM over traditional RTM or LRTM?
Vacuum Assisted Resin Transfer Molding (VARTM) Process
Vacuum assisted resin transfer molding (VARTM) is likely the most common acronym of all used in the discussion of low pressure closed mold reinforced composite molding. The often used VARTM acronym is most accurately applied to the process of vacuum infusion, that is where the composite is molded using a rigid mold to provide part geometry and a thin flexible membrane over the fiber, with outer atmospheric pressure compressing the fiber tight against the rigid mold surface. It should be noted however that VARTM simply means to add vacuum at the exit vent of the molding tool, thus any form of resin transfer molding in which vacuum is applied to the vent would qualify for the VARTM association. Often, the aerospace industry will have very high fiber volume composites molded within a rigid matched mold set in which the fixed cavity mold is clamped closed using a press and the resin injection pressures typically range less than 100 psi, yet could be as high as 600psi as used to fill the mold encapsulating the dry fiber within.
Differentiating the Applications
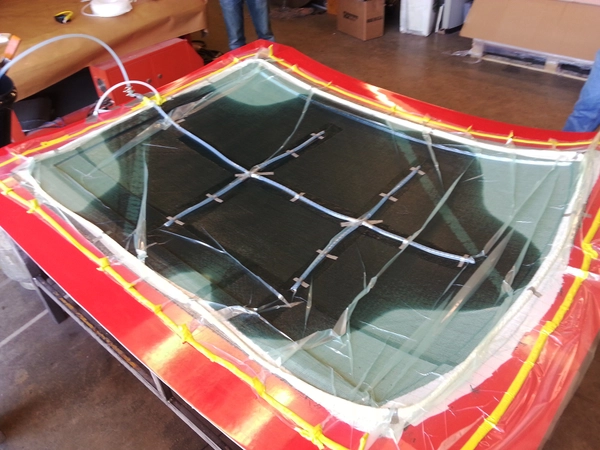
While the use of composites for applications such as the new Boeing 787 or some of the recent use of Space Shuttle or similar NASA applications continue to grow and are in use. The vast majority of composite molding applications fall into uses in the Automotive, Marine, Industrial and Recreational applications. In the Automotive industry the typical composite molding is supplied through the use of Sheet Molding Compound (SMC), then the group of remaining applications listed all rely on the Open Molding (Spray-up or Hand Lay-up) molding process often referred to as "contact molding".
The trend towards using "closed molding" in such as vacuum infusion (VARTM) or the resin transfer molding (RTM) with it’s most recent innovations as Light Resin Transfer Molding (LRTM), has been driven in recent years by both an interest in volatile organic compound (VOC) emission reduction and to lower labor content in the production processes which currently rely on the open molding technology.
As of this writing, while the interest is strong for conversion to the low pressure closed molding methods to avoid excessive VOC emissions and to reduce the need for skilled workers, the majority or the highest volume of parts produced still rely on the open molding methods. This is not to dispute all would likely agree the future clearly lies with the closed molding processes, the lack practical experience on the part of the molders and the added cost of tooling and raw materials used in producing the closed molded parts has continued to slow the growth of the conversion from open molding to closed molding over the years, as well up to today.
Focusing on the Most Common Applications
As mentioned above the most common applications are for Automotive, Marine, Industry and Recreational markets. The volume needs of the Automotive industry for the OEM production product generally leads to the need of the SMC process, yet for low volume, niche vehicle, applications often the volume is too low to justify the expenses of steel tooling as needed for SMC. So then the total industry overall volume outside of the SMC process for Automotive is the focus of interest here in this article.
Raw materials
In comparison, each of the focused processes and applications has commonality in the materials used for their composite molding. Each use typically a polyester or vinyl ester resin, most often fiberglass reinforcement having a ratio of fiber loading of 25 to 30% by weight of the total laminate as compared with the resin. It is this resin to fiber ratio which is most interesting and important to the strength and performance of the final molding.
It is to be understood that the corrosion, heat distortion temperature and general surface finish is driven primarily by the selection of the resin and while the mechanical strength is most attributed to the fiber reinforcement.
It is also to be noted that the fiber length is to a factor in the strength, that is to say short fibers typically less than 1" in length, impart poor strength, as compared to the same fiber in lengths of over 1" up to 3" in length. The fiber distribution in the crossection of the molded laminate is another critical factor for strength and performance. If the fiber is heavily loaded to one side of the laminate, then remaining laminate thickness will be made up of just resin which would be unreinforced and prone to cracking if flexed. It is to be noted that fiber loading of 30% by weight equates to only approximately 17% by volume, so it is technically possible to have greater than 80% of the laminate crossectional thickness to be only resin making for a generally weak laminate when flexing.
Comparing the Process Methods
The stage has been set in this article to understand, that all of the most common applications using composites hold in common the same basic resins and reinforcements. So in effect there is no real difference in materials used in a part molded as an "Open Mold or Contact Molding" to one of the same made using RTM, LRTM or VARTM / Vacuum Infusion molded part. The fact remains the resin and the fiber is basically the same for each process, so if the fiber to resin ratio where consistent and the fiber distribution crossectionally in the laminate were the same, then each of the process methods would yield the same molded part performance in the end. With the commonality of the materials in mind, then what differences are there in the parts molded in each of the different process methods.
Again, the Open Mold processes, as well, the RTM and LRTM process all have the same fiber loading ratio of typically targeting 30% weight fiber, 70% resin. The variant to the process methods is the VARTM or Vacuum Infusion process, in this method the fiber loading increases to typically 60 to as high as 70% by weight of the laminate with the remaining 40 to 30% being resin.
If then the VARTM / Vacuum Infusion process has much higher fiber volume and the mechanical strength is coming primarily from the reinforcement, it is then is the logical to expect the performance of the VARTM / Vacuum Infusion part to be different and it is. Yet, before we consider the difference let’s review the difference in the tooling as used for the VARTM in comparison to the RTM or LRTM molding processes.
Comparing the actual mold cavity of each process
In the open molding process there is only one mold surface so the actual part thickness is totally up to the operator to control in how much resin and fiber is applied to the surface of the mold. The operator can also affect the fiber to resin ratio, by manually adjusting the resin content in relation to the fiber. While the RTM and LRTM both have fixed cavity crossections inherent to the build of their match mold set, then glass to resin ratio are then effected by the type / mount of fiber loaded and the distribution of the fiber crossectionally in the laminate. In the VARTM process there is one rigid mold surface and the opposing mold half is a film on top of the fiber, the actual cavity is determined by the fiber thickness once the outer atmosphere compresses the fiber when a vacuum is created between the rigid mold surface the film over the fiber.
Required Strengths
Reviewing the fact that the vast majority of molded parts have over the years adopted the typical fiber loading of 30% by weight as sufficient for most all applications, variations of resins have then enhanced the fiber properties for specific needs of heat or corrosion, as well as, surface finish. The other factor that is common to the most applications is the need for "stiffness" or "flex modulus". Here in lies the issue with the VARTM process, by the fact that there is only one mold surface and the amount of fiber loaded upon that surface sets the part thickness, using the same fiber loading value per square area in the VARTM process as would be used for the other molding process, yields a much thinner laminate and thus a much more flexible laminate.